【成功案例】NI 有神操作!把設計可製造性檢查週期砍掉一半!
- Enlight Technology
- Dec 11, 2024
- 7 min read
NI利用Valor DFM 提升新產品導入與生產效率
在電子製造業,設計可製造性(DFM)檢查往往是個耗時的惡夢:「元件選擇有誤、間距不足、銅層問題...」等待最終檢查時才發現這些問題,工程師只能加班改圖。美國知名儀器大廠 NI 最近分享了他們的突破:透過改造 DFM 流程,不只將檢查週期從 4-5 天縮短至 1.5 天,更讓需要重新審核的元件比例從 59% 驟降至 2%。關鍵在於他們將 DFM 檢查前移,從設計初期就開始進行。
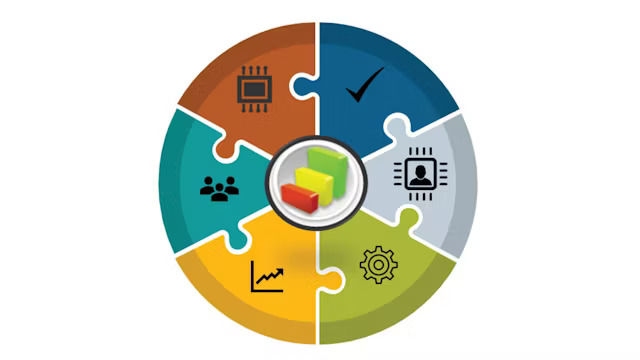
國家儀器公司(National Instruments)
超過 40 年來,NI(前稱 National Instruments)致力於開發自動化測試與測量系統,幫助工程師解決全球最棘手的挑戰。從數據與自動化到研究與驗證,NI 提供專屬且軟體連結的系統,滿足工程師與企業的需求。
總部:美國德克薩斯州奧斯汀
主要產品:Valor NPI, Valor Parts Library, Valor Process Preparation, Xpedition Enterprise
產業領域:電子業、半導體設備
成果總結
“經過六年的努力,上游專案的成果迄今完全符合預期,這在很大程度上得益於審慎的規劃、測試、學習以及對流程的修訂與優化。“— Chris Smith,國家儀器公司高級工程服務部門經理
縮短至一天的挑戰與實現
NI(前稱 National Instruments)從完全手動流程開始,逐步引入部分設計可製造性(DFM),最終完全擁抱 DFM 的優勢,並計劃全面採用。他們最初使用 Valor™ NPI 軟體進行最終 DFM 檢查,確保產品在釋放到製造階段之前達到標準。隨後,他們開始實施更上游的 DFM 流程,先是專注於早期的元件驗證,然後在設計過程中整合即時的 DFM 驗證。
此前,元件驗證和最終 DFM 檢查平均需要四到五天的週期時間。而採用新流程後,他們將平均 DFM 週期縮短了 60%,僅需一天半。此外,他們正在進一步擴展覆蓋範圍,預計最終能將 DFM 週期縮短至一天。
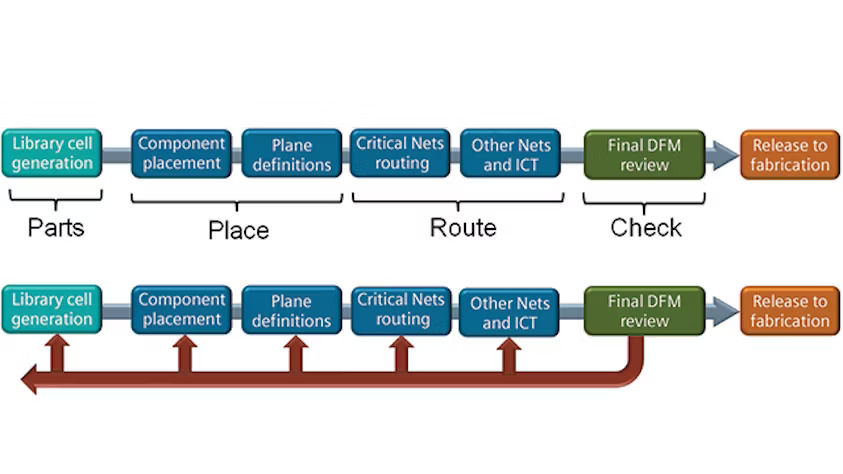
初步實施 DFM
NI 最初的 DFM(設計可製造性)實施方式與許多公司採用 DFM 軟體的初期步驟相似,如圖 1 所示。他們的初步應用主要是在設計釋放至製造階段之前執行 DFM 檢查,並在釋放前修正任何製造相關問題。為了更有效地利用資源,他們選擇創建一個通用的工程規則文件(ERF),適用於所有印刷電路板(PCBs)。這些規則由 DFM 工程師編寫和管理。
結果也與許多公司採用 DFM 時的情況類似。首先,提前發現製造問題並在釋放至製造商前解決這些問題帶來了巨大的效益,這避免了以往由製造商執行 DFM 時所需的額外迭代。然而,如圖 2 所示,內部執行 DFM 檢查還可以在 PCB 開發的所有階段釋放至製造之前發現潛在問題。
典型的錯誤包括:
元件選擇與生成
元件空間不足
銅層與電路網的問題
各種機械與製造規則的不符
電氣更新需求等。
雖然這些問題可以在內部發現,但對於需要重新設計的電路板,仍需投入相似的工程努力來應對由製造商執行 DFM 檢查而導致的問題。

創建全新的 DFM 流程
雖然在釋放設計至製造商之前進行 DFM 檢查帶來了顯著的益處,但仍需修正錯誤,有時甚至需要投入大量精力和時間,特別是當錯誤發生於設計周期早期時。為了解決這一問題,NI 在 2014 年與 Valor(Siemens Xcelerator 業務平台的一部分,包括軟體、硬體與服務)合作,決定將 DFM 流程盡可能提前,或者用 Valor 的術語來說,實現“左移”。
新 DFM 流程的目標是在設計的每個階段執行 DFM 檢查,以便在該階段發現並修正製造問題,而非等待到設計結束時再發現錯誤。預期結果是能在問題發生時立即解決,從而節省時間與成本。圖 3 展示了完整的新流程,該流程是分階段實施的。
創建新流程的第一步是在 NI 的業務需求範疇內定義 DFM。最終的 DFM 指南如表 1 所示。主要目標之一是利用現有流程與能力,從而將學習曲線和對現有設計流程的干擾降至最低。除了定義指南和規則,他們還為上游項目制定了一組目標。圖 4 展示了他們的四大主要目標。

第一階段
為了充分利用現有流程與能力,NI 決定分階段實施新流程。在第一階段,他們從設計時間線的最左端開始:元件驗證。這樣做的原因是元件錯誤會在設計過程中傳遞,影響設計的多個部分。元件驗證不當可能導致元件放置需重新調整,進而影響佈局、測試,甚至影響絲印與焊接掩膜,這些問題會大幅增加專案的時間成本。
在第一階段,NI 使用 Valor NPI 和 Valor Parts Library(VPL)執行元件驗證,並設置了三大目標:
同步符號、元件單元與邏輯創建:通過使用 VPL 確認同步性,NI 能夠提前數週發現元件問題,而這些問題在過去的流程中往往會被延遲發現。
創建新元件與修改元件的隊列:通過使用隊列,資料庫管理員可以驗證新增或修改的元件,確保一致性與準確性。
線上追蹤與定義最佳/認可元件:為了實現與技術同步及縮短週期的目標,消除對同一元件的重複審核,並快速識別未經驗證的元件是至關重要的。
使用 VPL 讓元件定義的驗證變得可能,包括供應商料號、元件單元以及焊接設定檔。在超過十億個 VPL 元件中,NI 將其本地庫中 21,000 多個元件與之匹配。將元件數量縮減至與 NI 相關的範圍後,他們能更快速地執行 DFM 檢查。
實施與成果
第一階段於 2014 年第二季度啟動。與引入任何新工具一樣,團隊中有部分成員對此舉的效益持懷疑態度。然而,NI 精確記錄了元件審核的比例以及專案設計週期的變化,持續觀察超過四年的結果,數據如圖 5 所示。
“結果顯而易見:元件審核的比例從原先的 59% 減少到僅 2%,相應的時間節省促使 DFM 週期時間縮短了 60%,同時也實現了減少 DFM 問題數量的主要目標。” — Chris Smith,高級工程服務部門經理

第二階段
第二階段於 2018 年啟動,目標是將 DFM(設計可製造性)擴展至更多的專案開發周期環節。其計劃如圖 6 所示,以迭代方式進行並測量其影響。
主要目標
確定資源與時間消耗最多的前 10 個 DFM 問題:這些問題的優先解決將帶來最大效益。
創建動態規則值:這些規則將匹配製造與組裝要求、專案的複雜性及設計師的需求。
實驗最佳報告量:測試報告的詳細程度,避免不必要的數據過載或報告過於模糊。
驗證改進源自 DFM 能力分佈的影響:通過控制案例驗證所有改進是否與 DFM 的分佈應用直接相關。
動態規則與流程控制
NI 利用 Valor 的分析定義管理器(ADM)創建規則,充分發揮其強大功能。ADM 支援製造與組裝,包括多供應商與多工藝需求。DFM 工程師可以根據製造商要求與設計複雜性選擇約束集(分類集),並能按專案動態選擇規則,而非僅遵循通用約束集。此外,ADM 還能與 XPEDITION™ 軟體集成,實現佈局過程中的即時 DFM 檢查。
NI 為了驗證流程準確性,設計了非生產性專案,並故意引入製造規則不符的問題以測試流程。他們對設計進行測試並將結果與預期進行比較,這一步驟幫助發現流程中的潛在缺口,減少實施中的變更需求,並提高了部署質量。
測試與改進
在完成前期工作後,第二階段的上游流程與設計團隊一同進行了測試,作為流程的 Beta 測試版本。在一年的測試期間,流程得到了改進,報告得到鞏固,規則集進一步優化。在 XPEDITION 上並行運行 DFM 的過程中,團隊發現這不僅僅是另一個工具,而是一個隨需應用的解決方案,可以定位潛在問題、交叉定位並解決問題,從而減少潛在的重新設計和後期更改。
到第二階段結束時,上游流程已準備好全面應用。
“此時,距專案啟動已六年,其結果完全符合預期,很大程度上得益於周密的規劃、測試、學習與流程修訂。” — Chris Smith,高級工程服務部門經理
結果與影響
圖 7 展示了結合第一階段與第二階段目標的完整上游執行流程。實施上游計劃的結果表明,該流程可以在元件驗證與設計階段發現並解決常見問題,相較於僅在設計結束時進行測試,節省了大量時間與成本。
通過動態規則選擇供應商與設計複雜性,DFM 報告中的製造規則不符數量大幅下降。最終,DFM 週期時間減少了 60%。

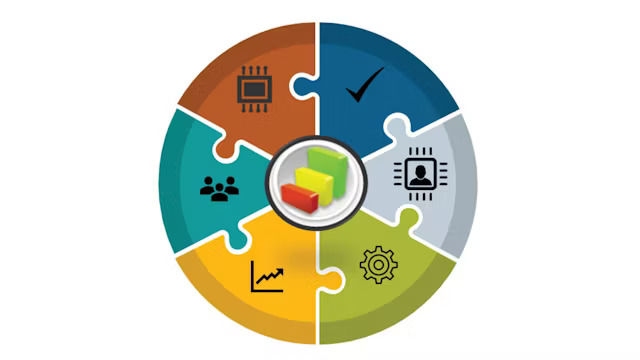
“重點總結:元件審核的比例從佔所有電路板元件的 59% 降至僅 2%。相應地,時間的節省促進了 DFM 週期時間減少 60%,並實現了減少 DFM 問題數量的主要目標。“— Chris Smith,高級工程服務部門經理,美國國家儀器公司
面臨的挑戰
減少完成完整 DFM 分析所需的時間
降低對產品設計的干擾
提升新產品導入與生產效率
增強團隊對結果承諾的信心
成功的關鍵
利用與 Siemens Digital Industries Software 的緊密合作關係
分階段整合 Valor NPI,而非一次性全部實施
採用系統化的推出方式,並監控與修訂流程以達到最佳效果
成果
DFM 週期時間縮短了 60%
元件驗證需求從 59% 降至 2%
Comments